The health and safety at work act (1974) outlines the main duty of care that both employers and employees have towards their workers and colleagues. Fundamentally the legislation helps ensure that working environments are safe, secure and clean, with all risks and hazards effectively managed, monitored and recorded.
Above all most working environments are different and will need a more tailored risk management procedure, but there are some primary tasks you can take to achieve a safer working environment.
Subsequently both your risk assessments and health and safety policies should devise a systematic procedure to effectively manage any risks. Here we have compiled a short list of the five most common risk reduction strategies.
1. Feedback
First and foremost it’s important to have ‘eyes everywhere’. One of the most time and cost effective ways to do this is by actively encouraging your workforce to regularly feedback any potential areas of concern they might have within their surroundings. Fundamentally this can be done with written forms or messages, however in most cases appointing a responsible person can be be most effective. They should carry out regular risk assessments and workstation inspections to help ensure that teams are complying with the company’s current guidelines. However, in instances that new hazards are brought to your attention, or if operating procedures, machinery or substances change you should update any existing policies at the first opportunity.
2. Eliminate
In some instances risks are temporary and can be eliminated before they cause a problem. In this instance you can prepare for temporary risks by investing in and regularly replenish good quality spill and cleaning resources. Here are a selection of products that may help with this.
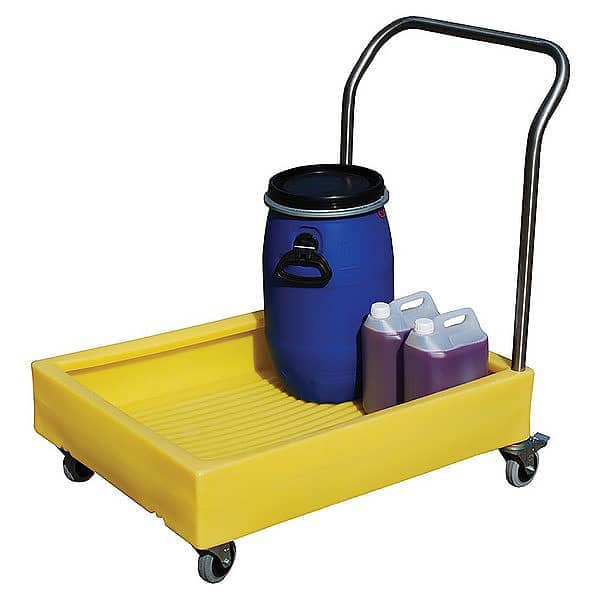
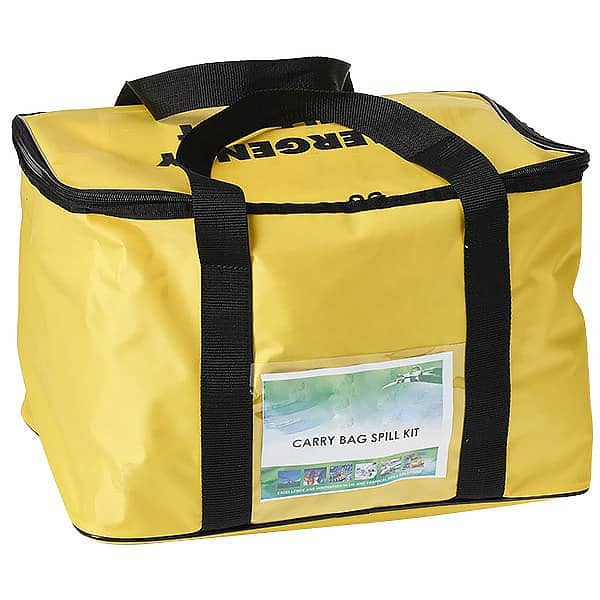
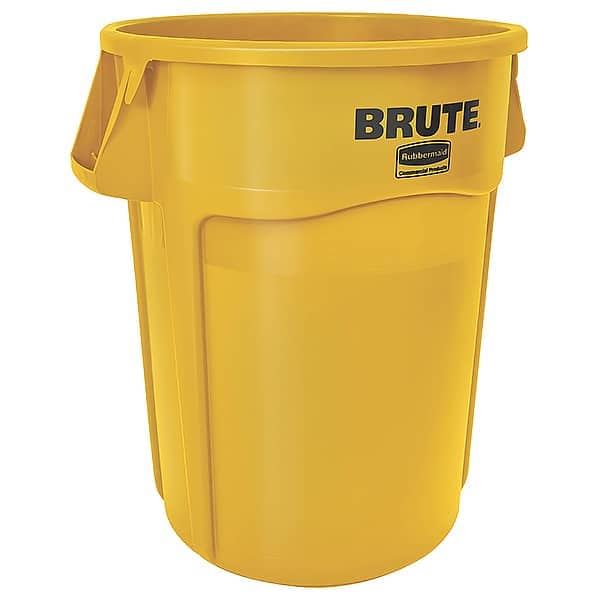
“If a piece of equipment is faulty or broken, repair or replace it immediately.” (HSE, 2019)
3. Isolate
Similarly, when it comes to unavoidable hazards it’s important to Isolate it from both your workers and any members of the public. This is done through signage, safe storage and temporary barriers.
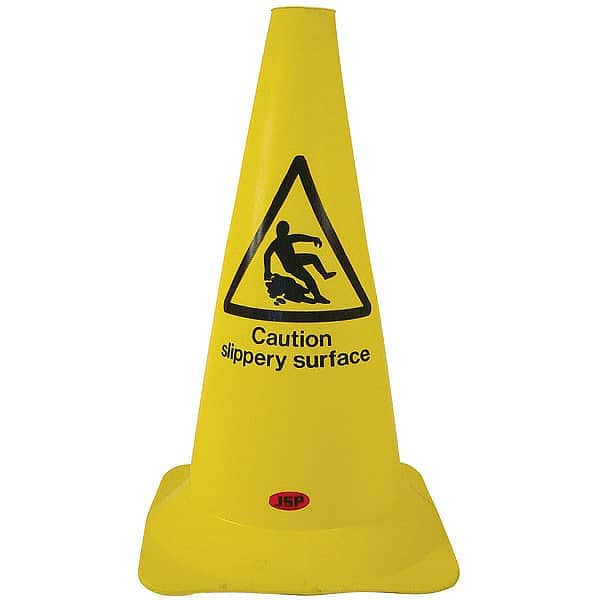
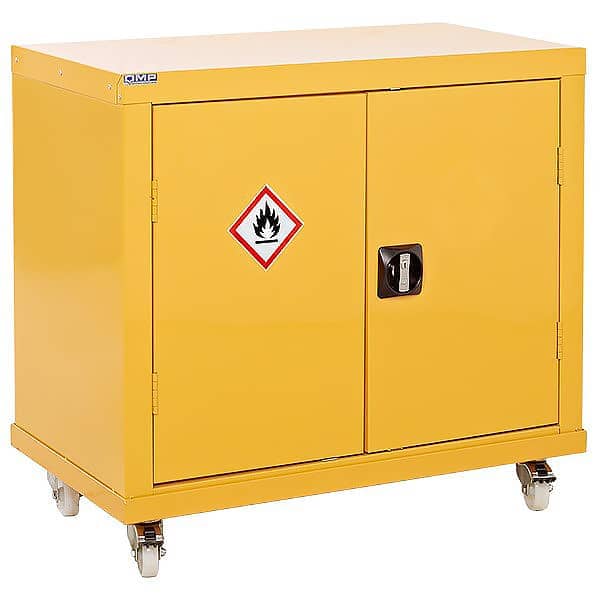
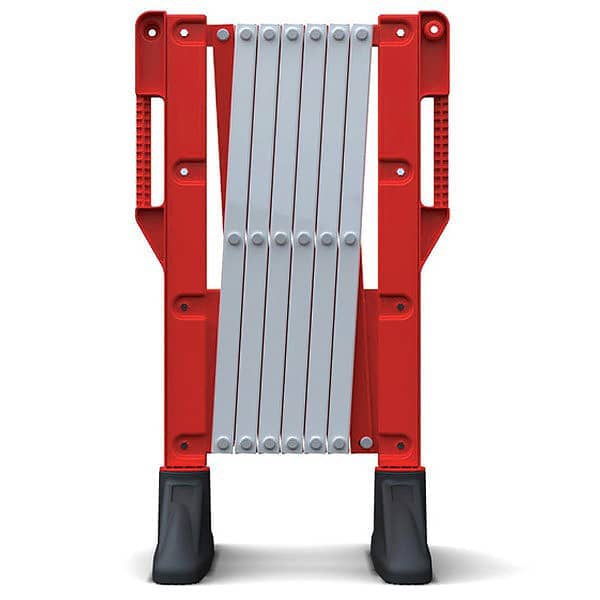
4. Restrict
The nature of some industries require employees to work in hazardous areas. Investing in personal protective equipment (PPE) is a low cost preventative measure to restrict the exposure of workers to hazards. The most popular PPE items are hard hats, protective eyeware, gloves and ear defenders. These tend to be available in different sizes and colours.
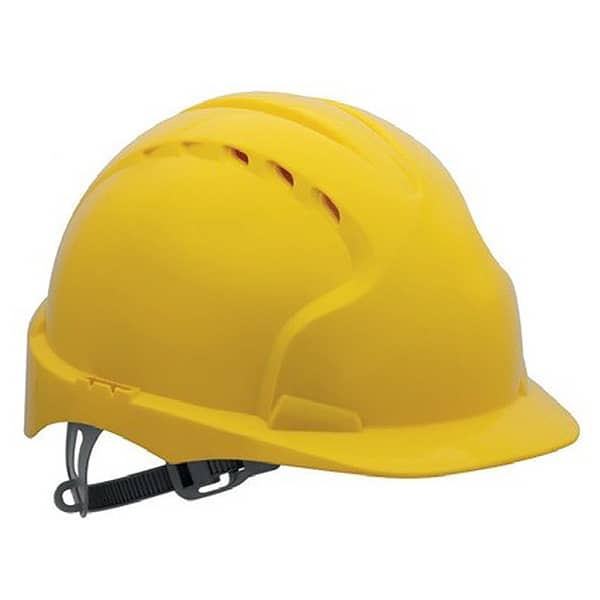
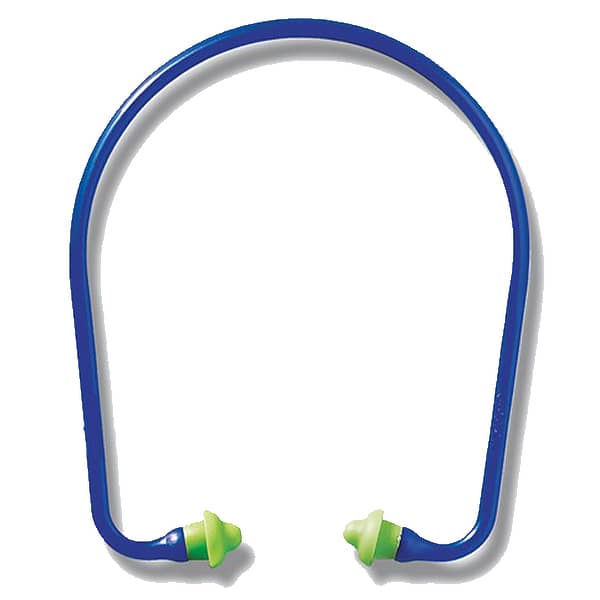
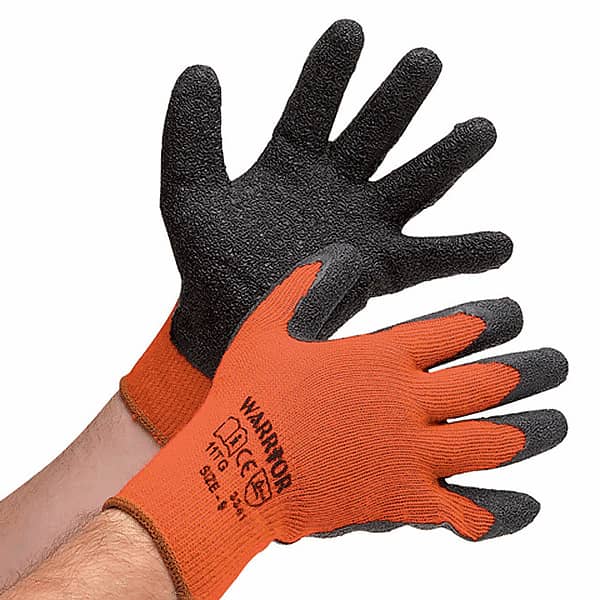
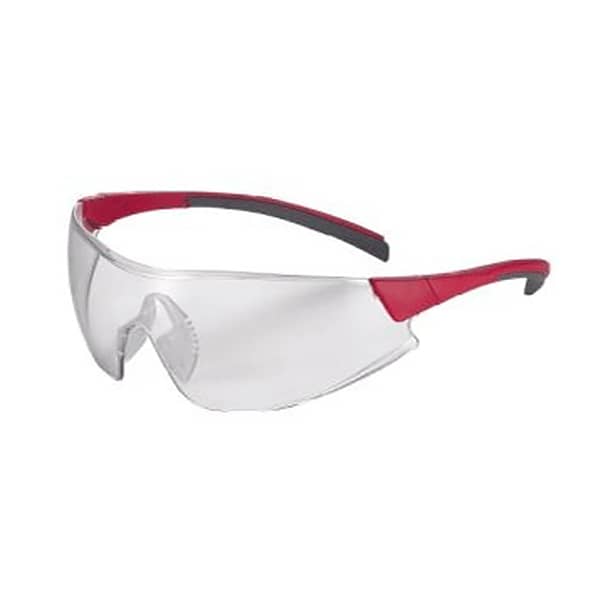
Providing your workforce with a PPE locker can increase the lifespan of their equipment. Coupled with this, they also assist with safe storage of equipment and can reduce expenses to the business in the long term.
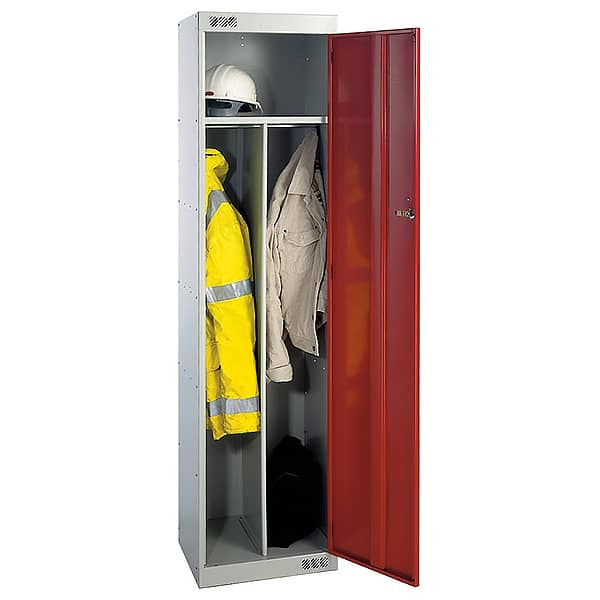
5. Educate
Educating to increase awareness takes little time but can decrease the number of workplace accidents. Many businesses hold meetings and training courses to educate on working in a safe manner. This time is useful to discuss any further tools and signage to assist with daily tasks. The most common items for this are trolleys, sack trucks and access equipment.
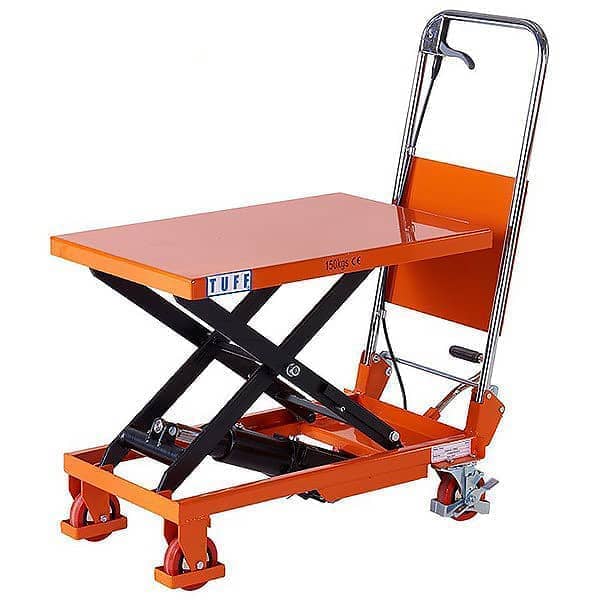
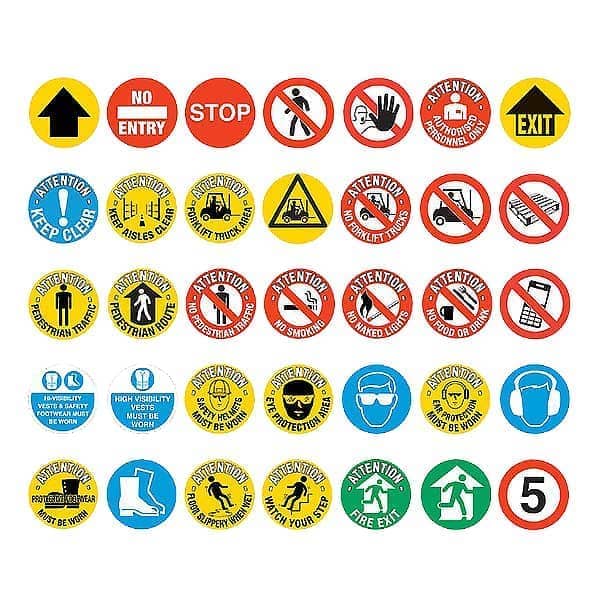
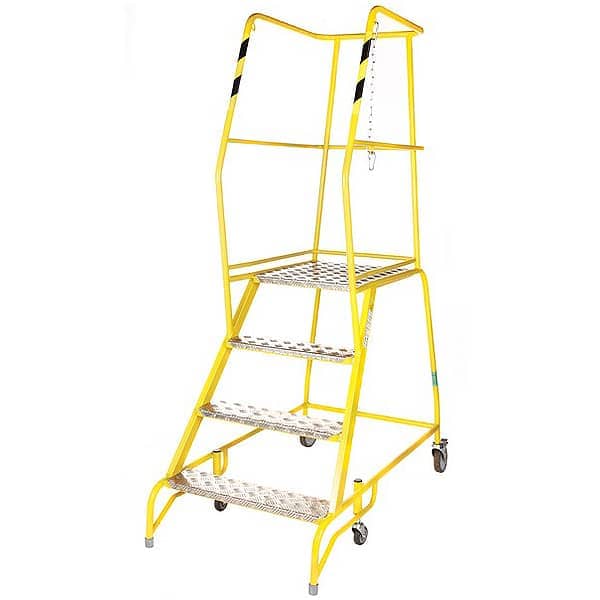
6. Record
Lastly, even in the safest places accidents and injuries are unavoidable. Therefore it is important to have all necessary resources in place to reduce the impacts on the person involved. A suitably equipped first aid kit and detailed record of the incident will help with this. Detailed accident reports can help with implementing measures to avoid similar injuries in the future, while ensuring that you comply with current RIDDOR regulations.
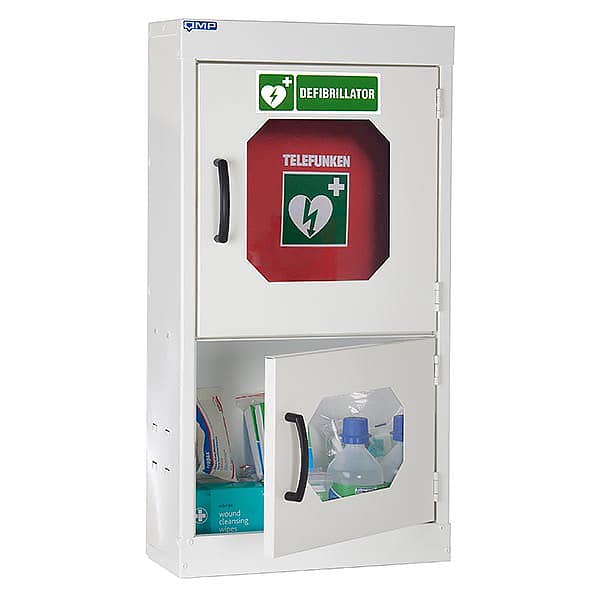
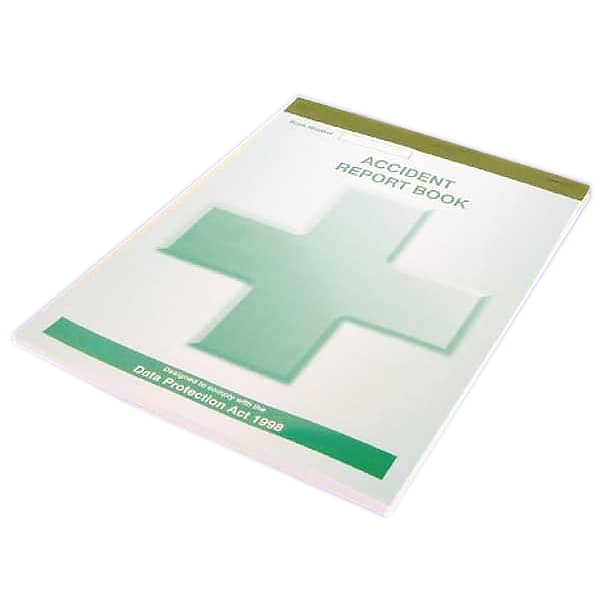
“Tiredness leads to accidents” (HSE, 2019). Give your workers regular rest breaks to help increase concentration and reduce the risks of accidents.
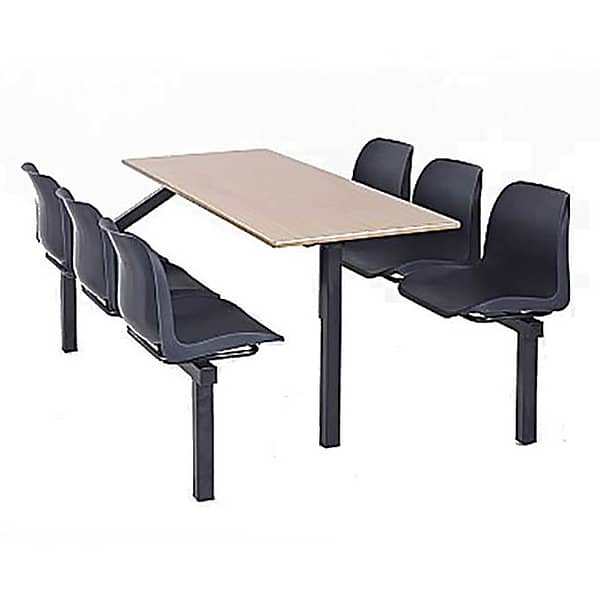